(Note: This story appears in the June 2021 issue of SE Magazine)
Lora DiCarlo’s products combine innovative technology — such as 3D printing — and alluring design led by its award-winning, in-house engineering team.
Touted as “the world’s most influential technology event”, the Consumer Electronics Show (CES) has been introducing the newest gadgets, tech and tech trends to attendees since 1967. And in its 50-plus-year history, there has only been one sex tech company to win the Innovation Award in Robotics.
Lora DiCarlo, the eponymous brand based in Bend, Oregon, busted onto the CES floor with its flagship product, Osé. After Lora DiCarlo’s strong and sensationalized start— the Consumer Technology Association, which organizes the CES, revoked the award and then re-awarded it with an apology and invaluable exposure for Lora DiCarlo. Sex tech companies are now allowed at CES in the health and wellness category.
“There is no ‘hand-off’ stage when a product concept is moved from mechanical to electrical or industrial engineering,” says Avery Smith, lead mechanical engineer with Lora DiCarlo. “Rather, with such a small team, each of us stays closely involved in the product development process from start to finish.”
STOREROTICA Magazine spoke with Smith about Lora DiCarlo’s robust, award-winning in-house engineering team and capabilities, processes and how they all make it all happen.
SE: How does the engineering team work together as a cohesive unit?
SMITH: We do a lot of brainstorming and problem solving as a group, so we are constantly communicating with each other. We all have different strengths and weaknesses, so it is really important to listen and share transparent feedback with each other. This open-door approach helps us avoid missed information or missed opportunities. It’s made us a very close team and we all really respect each other’s perspectives, even when creative differences arise on occasion.
SE: Can you walk me through the creative process from engineers to finalized product. For example, how did the Osé go from engineers’ computer to store shelves?
SMITH: We start with an idea, then we prototype it in- house to see how it turns out. We learn a lot from that initial prototype, but more often than not it ends up leaving us with more questions than answers. The road to the final concept from that point involves iterating on the design until we have something that meets or exceeds consumer needs! Once we have our final concept, there are manufacturing challenges to navigate. At that point, we work closely with our manufacturing partner to see that sufficient testing and validation are conducted to ensure a high-quality product.
“We start with an idea, then we prototype it in-house to see how it turns out. We learn a lot from that initial prototype, but more often than not it ends up leaving us with more questions than answers. The road to the final concept from that point involves iterating on the design until we have something that meets or exceeds consumer needs!” — Avery Smith
SE: How specifically, did you come to work with Oregon State University’s Robotics & Engineering Lab? What kind of expertise do they provide, resources, etc. Do they have any creative input?
SMITH: In 2017, our CEO and founder, Lora H. DiCarlo, reached out to John Parmigiani, head of Oregon State University’s Prototype Development Laboratory and pitched the idea of our flagship product, Osé. Their engineering lab decided to partner with us, and gave our team access to their rapid prototyping resources, such as their state-of-the- art 3D printers and machine shop.
Our team of engineers worked closely with students, professors, and doctors at OSU to incorporate microrobotic technology that would closely replicate the feel of human touch while stimulating the glans clitoris and the G-spot (or the urethral sponge) simultaneously. These resources were essential in enabling us to launch our first product as quickly as we did, by giving us the ability to produce initial prototypes in-house, and watch the product come to life in real time.
SE: What was your study about in relation to vulva anatomy? Was it more for internal (i.e. how has LD benefited from it) or external use (how does it benefit the adult toy industry at large)?
SMITH: I wrote a literature review that surveyed the existing dimensional data collected by the medical industry on vulva vaginal anatomy. The paper identifies the major studies conducted and attempts to provide a comprehensive overview of dimensional data collected. Unfortunately, one of the key takeaways from the review was the realization that there is a very limited amount of data available, and simply grouping it all together does not make sense due to the study to study variation. The sexual wellness industry at large would benefit from more raw data being collected and made available for independent statistical analysis.
SE: You mentioned product testing processes—can you expand on that, including any special equipment or engineering metrics used, etc.?
SMITH: We go to great lengths to correlate engineering metrics such as frequency, force, pressure, and sound, to user preferences so that we can continuously improve on our designs for a better user experience. Our in-house 3D printers are the most essential tools we have for quickly creating forms in order to test the fit and ergonomics.
We utilize a pressure gauge to measure efficiency and consistency in products like Osé and Baci, a sound pressure meter, and a thermal imaging camera for our Warming Collection.
“Our team of engineers worked closely with students, professors, and doctors at (Oregon State University) to incorporate microrobotic technology that would closely replicate the feel of human touch while stimulating the glans clitoris and the G-spot (or the urethral sponge) simultaneously.” — Avery Smith
SE: What is LD’s approach to sex tech?
SMITH: Lora DiCarlo approaches sex tech in a way that ultimately aims to empower people of all genders and orientations to explore their sexuality with positivity and confidence. We focus on creating unique products that elevate the user experience by incorporating new tech and clever engineering solutions. We always try to set apart our products by making sure that each maintains a unique ‘edge’ that other products don’t.
SE: What’s an example of mainstream tech you’re looking at/have looked at to apply to your own products and how was that tech incorporated/adapted?
SMITH: The neck that connects the shaft and base of Osé 2 is unlike any other dual stimulator we’ve seen. The internal wires had to be both flexible and durable, while holding their shape enough to create a stable, hands- free product. Most of us on the engineering team are new to the sex tech industry, so we’re always thinking about technology from mainstream products and how that innovation and functionality can be applied to sex tech.
For more information, visit loradicarlo.com.
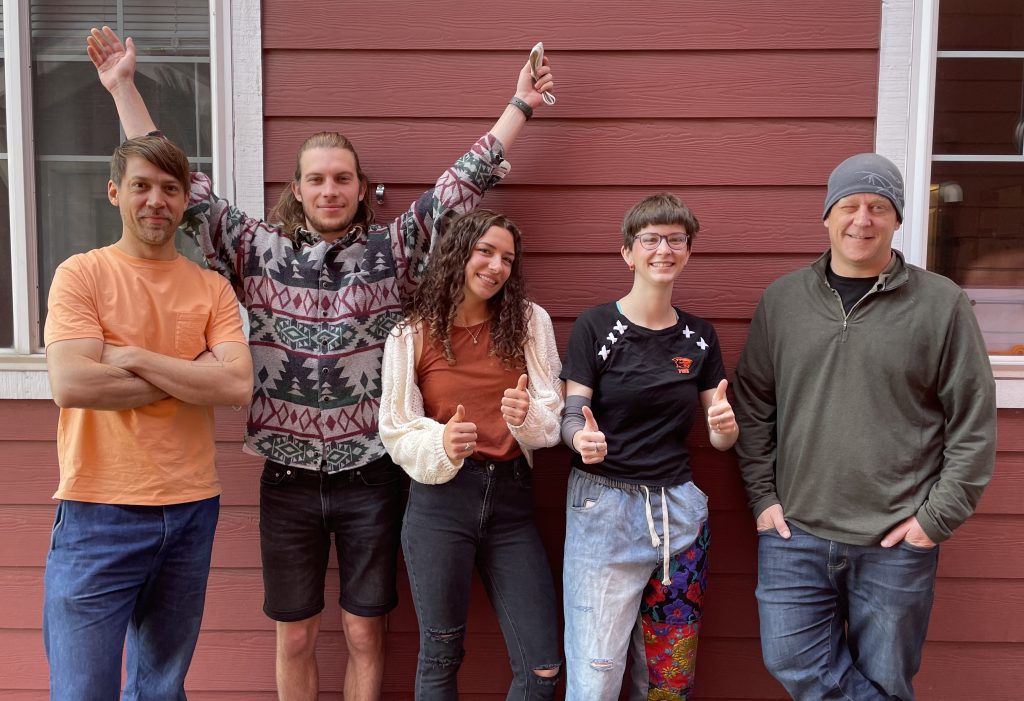
You must be logged in to post a comment.